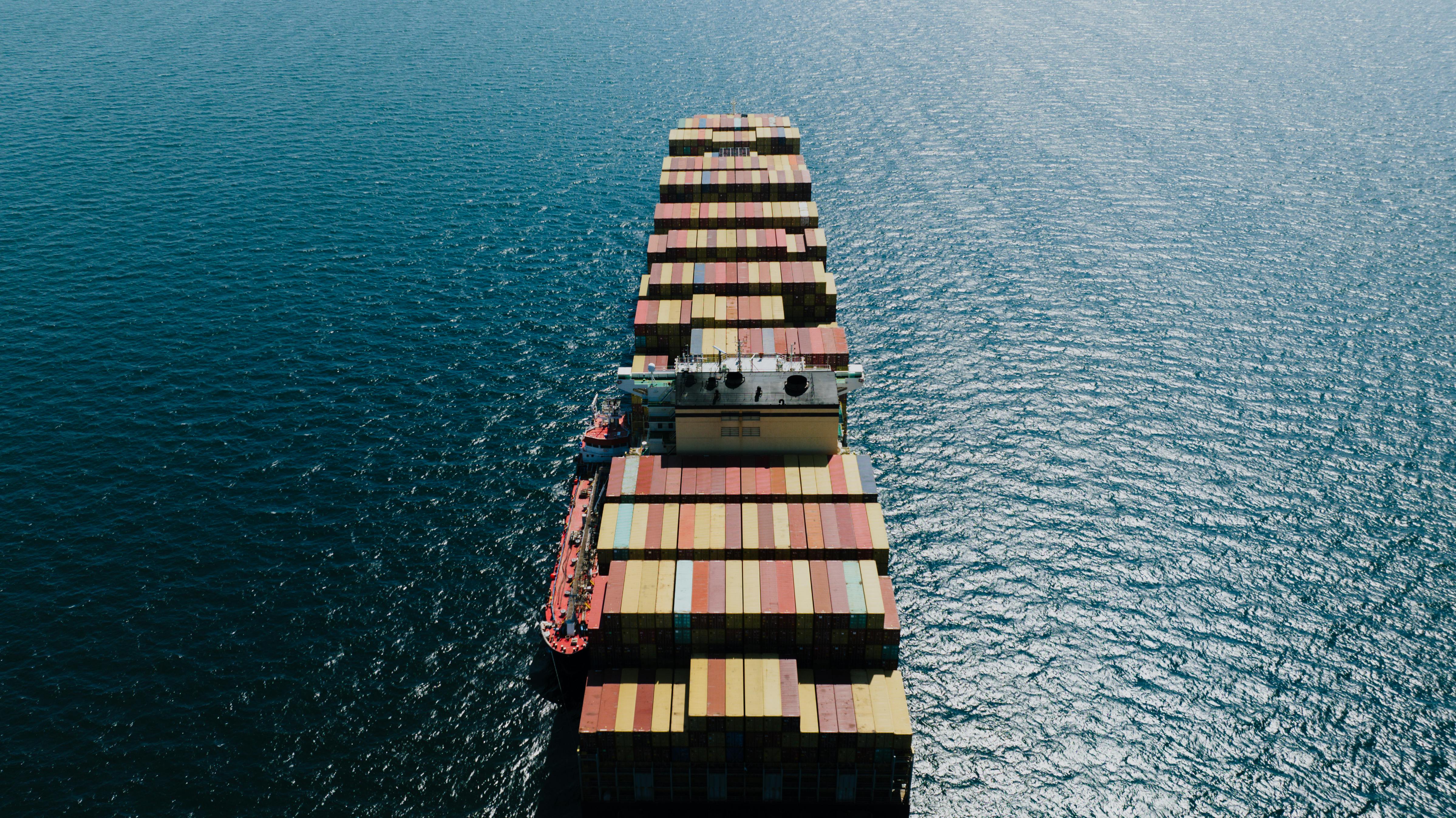
The 5 Hidden Challenges of Global Manufacturing That Could Be Affecting Your Margins
Global manufacturing is an important part of today’s economy since it allows companies to expand into new markets while generating profits. However, these opportunities come with challenges that, if not handled, could reduce profit margins over time.
With growing competition and changing economic conditions, manufacturers must negotiate an unpredictable market in order to preserve their financial stability. This post explores 5 hidden challenges that manufacturing companies face in distant markets and shares advice on how to keep producing efficiently.
How is Globalization Changing the Manufacturing Industry?
Globalization has brought major changes to manufacturing, with more competition, shorter market periods, and higher consumer demand. Companies now face the challenge of creating innovative products that stand out in diverse global markets. Here are some of the most important changes:
1. Dealing with Market Volatility
The global manufacturing sector has been hit by changing demand and rising production costs, contributing to a 1.76% decline in growth, according to StartUs Insights. To reduce these pressures, companies optimize processes and invest in cost-saving technologies, to respond quickly to changes and manage rising production costs.
2. Focusing on Workforce Needs
As manufacturing systems grow more complex, companies worldwide are expanding their workforce to meet production demands. A report by StartUs Insights indicates 622,000 new jobs, bringing the global workforce to 13.2 million, a sign of the industry’s resilience and growth despite broader economic challenges.
3. Prioritizing Innovation
The sector’s strong commitment to research and development is evident, with 139,000 patents filed across areas like automation, sustainability, and quality control, according to StartUs Insights. This focus on innovation drives efficiency, reduces costs, and improves product consistency, positioning companies to better meet global market demands.
5 Hidden Challenges Affecting Manufacturing Profits
The expansion of the Lázaro Cárdenas port is a key initiative for Mexico, bringing considerable benefits to its economy and global standing. Key aspects of this deveIn the global manufacturing industry, certain critical challenges often go unnoticed but can impact profit margins if not managed carefully. These five hidden challenges present risks to efficiency and profitability across the industry:
1. Balancing Inventory and Project Demands
In manufacturing, keeping inventory levels balanced is essential to meet customer demand without overstocking, which increases storage costs. As demand changes, maintaining this balance becomes more challenging, especially with supply chain disruptions or shifting production needs.
Many manufacturers address these complexities using digital systems, such as ERP, which integrate real-time data and automated processes, allowing for flexible decision-making to keep projects on track and within budget, even when conditions shift suddenly.
2. Reducing Supply Chain Disruptions
Manufacturers today depend on complex global supply chains, which are vulnerable to disruptions from political events, environmental issues, and changing trade policies. These interruptions can lead to cost increases, quality concerns, and delays in product delivery.
A recent study by Automation World revealed that 78% of manufacturing leaders see supply chain disruptions as a top concern. To address this, many manufacturers diversify suppliers and use digital tracking tools for greater visibility, such as warehouse management software (WMS) or dashboards, enabling them to respond quickly when issues are identified.
3. Managing Production Limits and Capacity
As manufacturing operations expand, ensuring smooth production flow without interruptions is crucial to meet order deadlines and maintain customer satisfaction. Capacity limitations often lead to delays and lost revenue opportunities.
By tracking performance indicators such as lead times and using ERP systems, manufacturers gain insights into production, inventory, and sales performance. This integrated approach helps identify weak points and make adjustments to increase capacity for larger orders.
4. Aligning Automation with Strategic Planning
Automation can bring considerable cost savings and efficiency improvements, but it requires strategic planning and serious investment. Beyond the initial cost, companies must train staff to operate automated systems effectively.
When implemented successfully, automation minimizes manual errors, accelerates production lines, and optimizes inventory tracking. However, balancing these benefits with initial expenses is a common challenge for many manufacturers.
5. Solving Workforce Shortages
A decrease in the pool of skilled labor has become a major issue for manufacturing, especially as automation and new technologies require specialized expertise. A Deloitte study, cited by Today’s Medical Developments, projects that 2.1 million manufacturing jobs may go unfilled by 2030.
To reduce this deficit, manufacturers are investing in training programs and using augmented reality (AR) for real-time guidance, helping less experienced workers adapt more quickly.
How to Adapt to Challenges in Global Manufacturing?
Considering all the hidden changes in the manufacturing sector, companies are considering new production locations. Rising operational costs in traditional hubs and increasing demand for shorter, more responsive supply chains are encouraging manufacturers to move production closer to primary consumer markets.
In North America, manufacturing has become more attractive due to cost benefits, logistical efficiency, and the increasing expense of offshore production in countries like China.
Advantages of Localized Production in North America
For companies targeting U.S. markets, setting up production within North America brings the following main advantages:
- Reduced Shipping Times: By minimizing the distance between production facilities and consumer markets, companies can reduce the time it takes for products to reach customers.
- Lower Transportation Costs: Shorter supply chains reduce shipping expenses, helping companies keep costs down and improving profitability.
- Increased Flexibility: Local production allows companies to respond more effectively to shifts in demand, maintain high-quality standards, and adapt quickly to market needs.
Learn about manufacturing opportunities in Mexico for US companies to reduce costs and improve supply chain efficiency.
Why Is Mexico the Next Strategic Manufacturing Hub?
Mexico, in particular, has been recognized as an attractive alternative to distant manufacturing hubs such as those in Asia, thanks to its proximity to the U.S., competitive labor costs, and well-developed infrastructure.
For companies looking to set up production in Mexico as their next manufacturing destination, a few specific advantages include:
- Proximity to U.S. Markets: With reduced transit times and easier logistics, Mexico provides U.S.-focused companies with a shorter supply chain, making production more cost-effective and responsive. These reasons make manufacturing in Mexico a smart cost-saving choice for your business.
- Trade Agreements: Through agreements like the USMCA (United States-Mexico-Canada Agreement), Mexico offers manufacturers favorable trade terms, reducing tariffs and streamlining the cross-border movement of goods within North America.
- Support from Shelter Service Providers: To streamline entry into the Mexican market, many manufacturers collaborate with shelter companies, such as TNC. These organizations help companies comply with local labor laws and environmental regulations, simplifying compliance and optimizing operations.
- Highly Skilled Workforce: Mexico’s manufacturing strength is based in a skilled workforce prepared to perform across diverse industries. With expertise in modern production methods, this talent pool helps to improve efficiency and ensures high-quality products.
- High Manufacturing Standards: Mexico’s robust industrial sector meets high-quality production requirements, making it a viable alternative to distant offshore locations.
Respond to Industry Challenges with TNC’s Manufacturing Solutions
Many companies overlook critical challenges in global manufacturing until they disrupt key operations and reduce profitability. By recognizing hidden issues, such as supply chain disruptions, inventory control problems, and workforce shortages, businesses can take corrective steps to minimize risks.
At The Nearshore Company, we work hand in hand with our clients to provide customized solutions that help businesses get over these obstacles, especially for those manufacturing in Mexico. With expertise in manufacturing services, operations, and 3PL, we ensure that your manufacturing runs smoothly in certified facilities staffed by highly qualified experts.
Download our free guide on identifying hidden costs in your supply chain to start reducing unexpected expenses and improving overall efficiency.