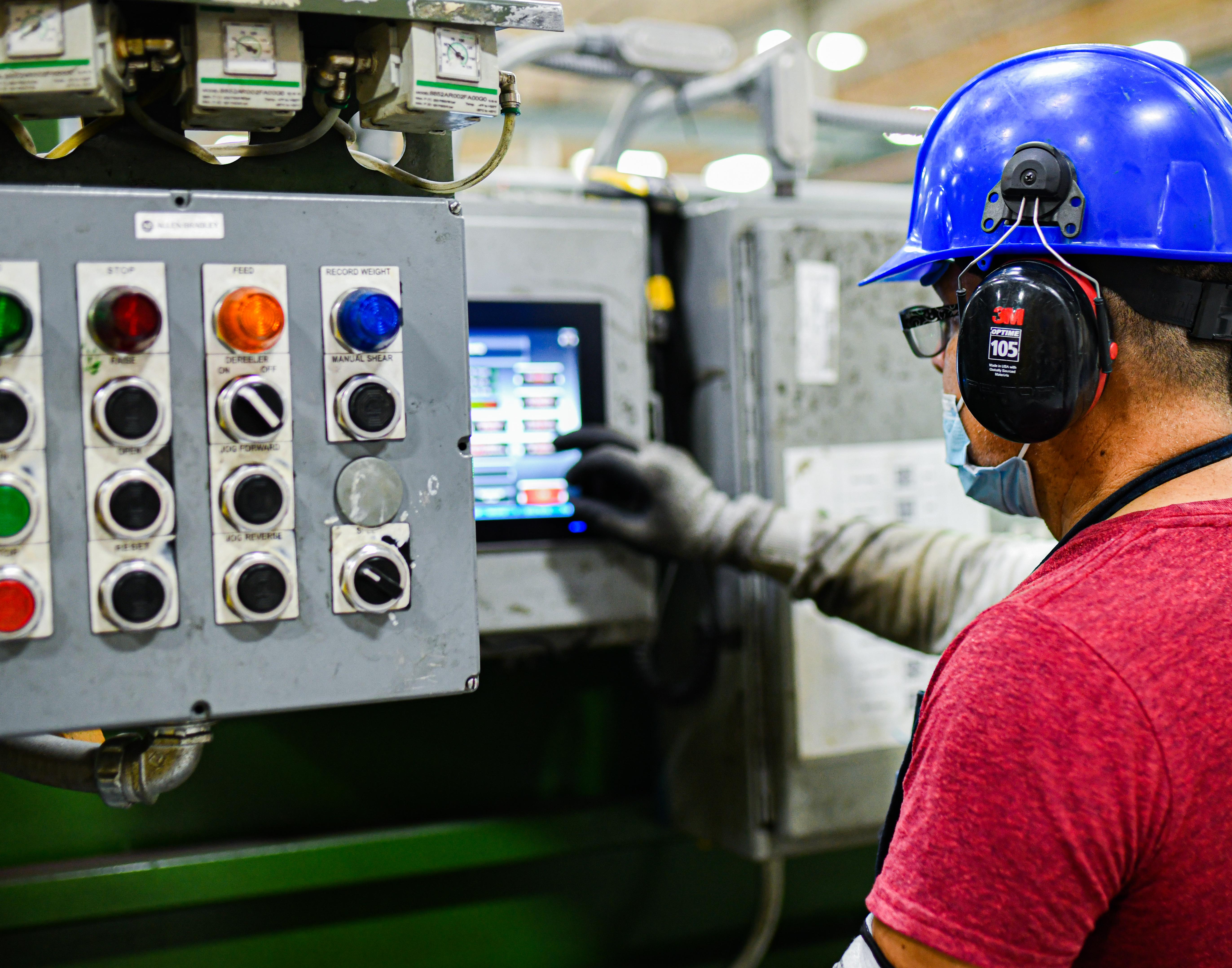
Is It Time to Rethink Your Supply Chain? Discover How Leading Companies Do It
Supply chain optimization is a critical factor in the success of today’s leading companies. As global markets and logistical challenges grow more complex, businesses are re-evaluating how to make their supply chains more efficient and cost-effective.
A well-optimized supply chain reduces operational expenses and improves quality and availability, providing companies with a competitive advantage. This post explores how optimization strategies can transform supply chains, allowing businesses to build long-term success while maintaining quality.
What is the Process of Supply Chain Optimization?
Globalization has brought major changes to manufacturing, with more competition, shorter market periods, and higher consumer demand. Companies now face the challenge of creating innovative products that stand out in diverse global markets. Here are some of the most important changes:
Supply chain optimization is about refining each component of the supply chain to operate with higher efficiency, reduce expenses, and maintain consistent quality standards. The process requires a structured approach to ensure that all supply chain operations align with the demands of today’s competitive market.
Companies generally structure this optimization into three main stages:
1. Design
This phase is focused on creating a reliable supply chain base, considering where to locate facilities, establishing efficient routes for product movement, and setting long-term goals such as demand planning and resource distribution. A well-planned network design allows products to flow smoothly between suppliers and customers, reducing potential disruptions.
- Example: A company might choose to place warehouses closer to key customer regions, reducing delivery times and minimizing transportation costs.
2. Planning
This stage focuses on aligning resources like inventory and transportation with anticipated demand to maintain product availability by synchronizing production and delivery schedules.
Strategic planning allows companies to respond to demand fluctuations efficiently, balancing supply levels to avoid overstocking or shortages.
- Example: A retailer might adjust inventory levels based on seasonal demand, increasing stock before the holiday season to avoid shortages and meet customer needs.
3. Execution
This phase is where plans are put into action with systems that support day-to-day operations, such as inventory control, transport management, and order processing. Effective execution depends on real-time tracking and responsive systems, enabling companies to adapt quickly, meet customer needs, and uphold high supply chain standards.
- Example: A company might use real-time inventory tracking to monitor stock levels, allowing them to restock popular items quickly and avoid potential delays in order fulfillment.
Learn 3 proven strategies to start manufacturing in Mexico for growth and efficiency.
Why is Supply Chain Optimization Important?
With the complexity of global logistics and rising customer expectations, companies that focus on optimizing their supply chain can more effectively manage disruptions, control costs, and respond quickly to market changes.
The following points reflect the main reasons why optimizing the supply chain is necessary for any company trying to succeed in an unpredictable market:
- Meeting Customer Expectations: Modern customers demand fast and efficient service, which requires companies to refine their supply chains constantly. Optimized processes ensure precise, consistent deliveries that align with customer standards.
- Gaining Competitive Advantage: A well-optimized supply chain improves a company’s ability to respond to market changes. Businesses that minimize delays and improve service quality can build strong customer loyalty and secure an advantage over competitors.
- Improving Operational Agility: Adaptability is key for handling unexpected changes in demand or supply chain disruptions. Visibility has become a priority for 55% of manufacturing companies, according to Fictiv, which allows businesses to anticipate these changes and keep operations running efficiently.
- Supporting Sustainability Initiatives: As environmental responsibility becomes a priority, companies are optimizing supply chains to reduce their impact. Consolidating shipments, reducing waste, and sourcing locally help make operations both efficient and eco-friendly.
Read about how nearshoring can support manufacturing sustainability for your company and optimize supply chain efficiency.
What Are the Benefits of Supply Chain Optimization?
Supply chain optimization is about improving how the supply chain works to make it more effective and capable of responding. By focusing on key improvements, companies can gain important benefits such as stronger operations and greater long-term profitability.
1. Reducing Inventory Costs
By aligning inventory with real demand and streamlining repetitive tasks, companies can cut unnecessary expenses. Improved logistics planning and strategically located facilities also help avoid excess stock and reduce transportation costs.
2. Increasing Profits and Revenue
A well-optimized supply chain helps increase process speed and reliability, ensuring products reach customers on time. This efficiency boosts customer loyalty and allows businesses to get faster returns on investment, which in turn helps both revenue growth and profit levels.
3. Improving Supplier Reliability
Real-time digital tools make it possible for companies to monitor supplier performance in real-time, facilitating improvements and quicker response times. Additionally, sourcing suppliers closer to production hubs minimizes delays and improves operational and production efficiency.
4. Supporting Supply Chain Communication
An integrated supply chain promotes better communication and mutually beneficial relationships between suppliers, partners, and third-party vendors. Access to shared, real-time information helps teams to make proactive decisions, building trust and stability across operations.
5. Maintaining High Quality Standards
With optimized supply chains, quality control becomes a central focus from sourcing through delivery. Placing quality checks at critical points minimizes waste and aligns all processes with the company’s quality standards, ensuring consistency and high quality at every step.
What Can Companies Do to Improve Their Supply Chain?
Companies can implement a variety of strategies to refine their operations and gain a competitive edge in the market. Here are some key actions they can consider:
1. Embrace Global Vision with Local Action
Businesses should focus on global sourcing opportunities while adapting processes to local market needs. Balancing international resources with local investments in technology, inventory, and infrastructure minimizes logistics costs and contributes to environmental sustainability, especially by operating close to core markets.
2. Establish Planning Capabilities
Effective planning allows companies to prepare for demand shifts and potential disruptions. With advanced forecasting tools and scenario planning, teams can anticipate changes and adjust inventory and capacity levels accordingly, reducing the risks associated with unexpected fluctuations.
3. Use Data Analytics for Decision-Making
Data analytics provides valuable insights into the purchasing process, production, and customer demand patterns. With advanced tools like artificial intelligence, companies can generate real-time insights that facilitate decision-making, allowing for immediate adjustments that keep operations on track.
4. Increase Automation
Automation minimizes manual tasks, simplifying inventory management, order processing, and logistics. A centralized system for tracking these functions provides more control, allowing companies to manage resources efficiently and focus on strategic growth.
5. Negotiate with Suppliers for Better Terms
Regularly revisiting supplier agreements helps companies maintain competitive pricing and adapt to market changes. By benchmarking supplier terms, businesses ensure they receive the best value and can sustain cost-effective supply chains.
6. Consider the Proximity of Key Suppliers
Reducing physical distances between suppliers and production facilities leads to faster response times and lower transportation costs. In fact, according to Fictiv, 51% of manufacturers are now interested in nearshoring, moving operations closer to North America—such as Mexico or Canada—to improve delivery times and cut logistics expenses.
Learn about manufacturing opportunities in Mexico for U.S. companies and the benefits of geographic proximity.
Find Expert Solutions in Supply Chain Optimization with TNC
In today’s global market, supply chain optimization goes beyond efficiency to help companies move closer to key markets, allowing faster response times and reduced costs. By moving operations near productive regions, companies gain the flexibility needed to quickly adapt and consistently meet customer demands.
At The Nearshore Company, we specialize in building strong, responsive supply chains by focusing on geographic proximity and operational flexibility. As manufacturing companies expand and face new challenges, strategies focused on location, efficiency, and resilience are essential for building long-term success.
Get our checklist on how to improve your supply chain and start optimizing for efficiency, flexibility, and proximity to key markets.